An open-source & low-cost geodesic dome system

Self-build as a social tool: Communities need collective spaces to gather for group activities and social support. The lack of a collective space to meet, discuss and perform group activities, especially at the early stages of the development of the community, can generate negative consequences in the future. Self-build can be a powerful social mechanism for strengthening communities. Examples of these communities are families, neighbours or young people in need of spaces for developing creativity, social actions or educational activities.
John Turner in his book “Freedom to Build” estimated that almost one third of the world’s dwellings are constructed by amateurs, their future occupants, with no architect intervention. Despite this staggering figure, architects and designers have paid little attention to self build and it has been normally considered a sort of natural phenomenon outside architects competencies and normally circumscribed to vernacular architecture using traditional and labour intensive construction methods.
The researched initiatives described in this article use self-build as a social tool for strengthening communities. Some of them focus on creating innovative construction methods which reduce intensive labor and facilitate the adoption from non-skilled self builders, such as the Segal method and Wikihouse Rio. Others initiatives design complex social mechanisms to empower communities in creating their own built environment, such as the traditional Barn Raising during the colonisation of North America and Recetas Urbanas, where the latter also seeks for new ways to apply and understand regulations.
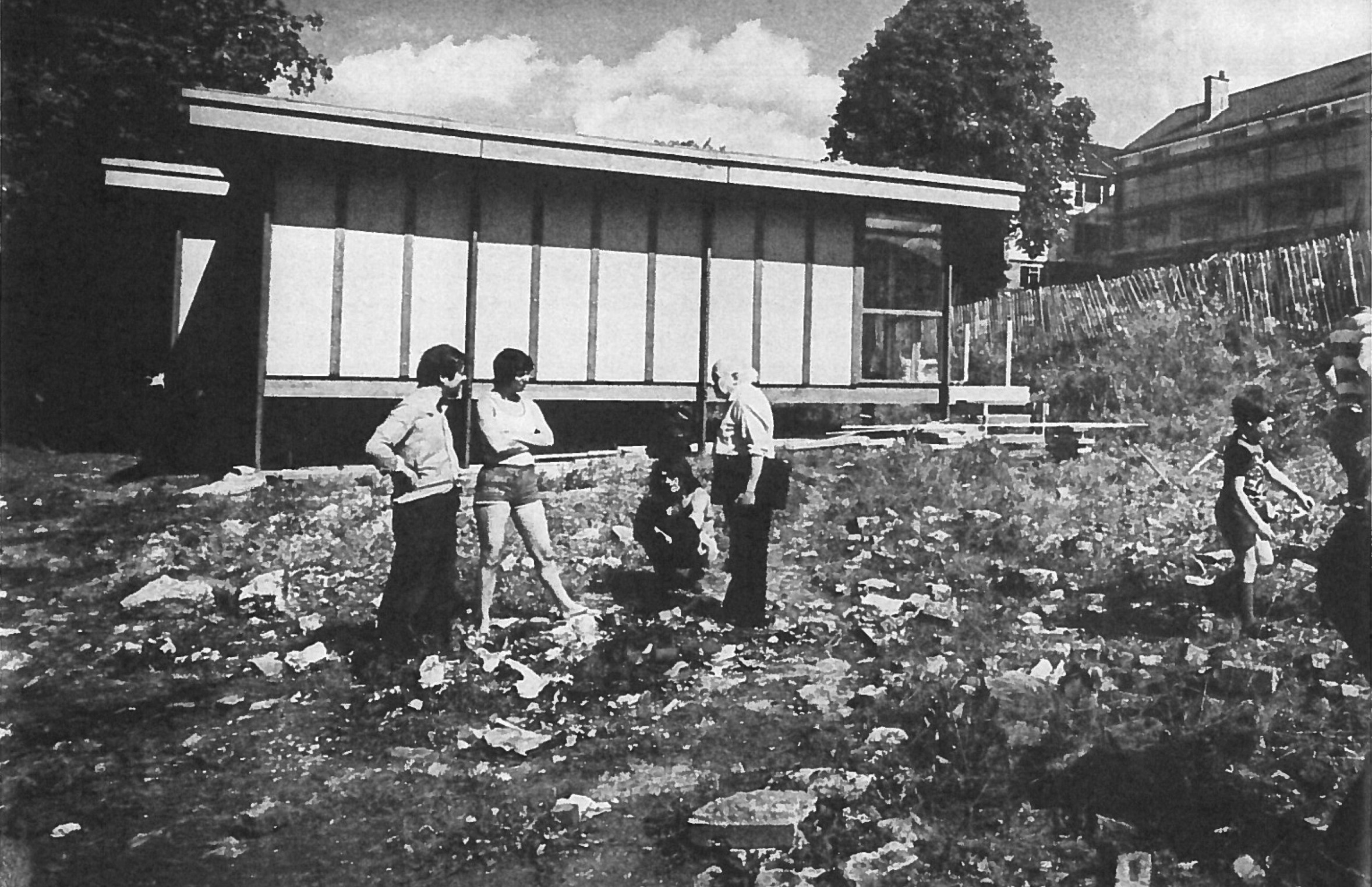
Segal method
This simple and yet sophisticated timber frame construction system developed by German- born architect Walter Segal in the 1960’s gained some popularity among individual self-builders in the 1970’s. Thanks to British anarchist architect and writer Colin Ward, who introduced Segal to Lewisham Borough Council’s planning authorities, the method evolved into a great tool for social housing provision and community development.
Lewisham Borough Assistant Architect Brian Richardson, together with Walter Segal developed a system in which people in need of social housing were able to take part in a collective self-build housing scheme regarding their lack of skills, age or income level. The Council picked seven plots that were unbuildable using traditional construction techniques. They formed random groups of self-builders taken from the Council housing waiting list and selected by ballot. More than twenty years later these self-build housing schemes show an unprecedented level of community engagement and improved social and economic conditions. Since then, the method has been applied in larger scale community projects such as civic, day care and skill centres.
Wikihouse Rio
Wikihouse is an open source construction kit by “00 [zero zero]” studio that enables anyone to create, download and build houses. This houses can be easily fabricated using a Computer Numerically Controlled (CNC) router and assembled without the need for formal training. Wikihouse was brought to Rio in 2014 in collaboration with Dharma agency and Estúdio Guanabara as a way to empower youth from suburbs and favelas of the city of Rio de Janeiro and enable creativity and active citizenship. This initiative combines the use of digital fabrication techniques and an open source construction system to enhance community youth development and their quality of life. WikihouseRio is at its early stage, however shows great potential as a social integration mechanism. In March 2015, they built the first wikihouse in Latin American and they are continuously working on enabling access to more open source CNC machines.
Barn raising
Barn raising is a collective action in rural communities in which the barn of one farmer is constructed collectively by all the members of the community. It normally takes a couple of days in which the entire community is involved: men participate in the build, women cook, children watch and teenagers bring tools. Barn raising was common during North American colonisation as it was almost impossible for a single family to self-build such big structures in a reasonable time frame. Current building technologies and modern labour division have made barn-raising redundant and impractical but in some rural communities in United States and Canada it is kept as one of their most important community traditions and engaging social activities.
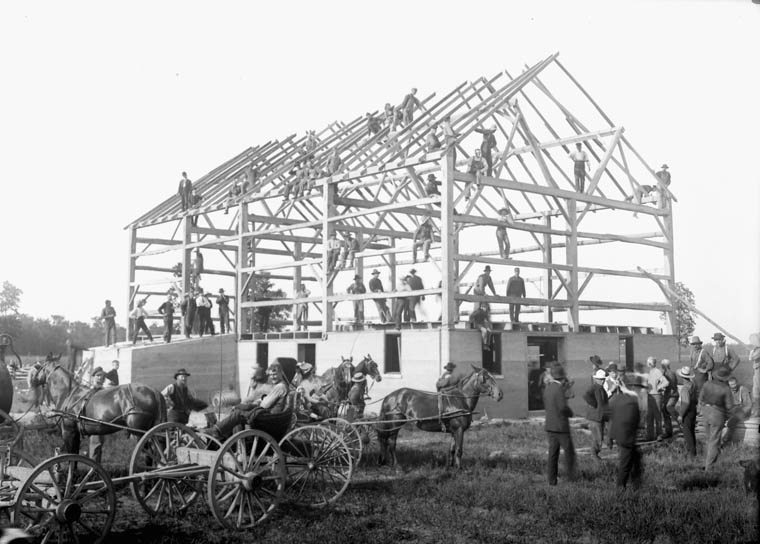
Recetas Urbanas
In 2004, Recetas Urbanas studio was founded by Santiago Cirugeda, architect and activist from Seville (Spain). They carried out numerous occupation projects, prosthesis and opening-up of spaces to the public. Santiago Cirugeda purported with the concept of “alegality”; referring to occupation or construction strategies that use methods which are neither regulated nor prohibited, inotherwords,“alegal”.Theycanbedefined as occupations or constructions to empower citizens to create their own build environment by taking advantage of those areas where regulation does not exist or is unclear.
Lately Recetas Urbanas have been working on self-building classrooms for primary and secondary schools. They develop self-building workshops to perform construction by taking advantage of the energy of students, families and teachers. The reuse of public and private materials keep the cost low while supporting recycling. These social-educational projects created strong links within the school community while always promoting working in a safe and creative environment.
Self-build temporary collective spaces
Frequently, years will go by before the communities can take care of their collective space needs. Usually, the goal of community self-build projects is a permanent building which requires a considerable amount of planning and financial resources. By self- building a temporary collective structure the community could enjoy all the benefits of a collective self-build project which can be started in a very early stage of the community development and ensure a healthy development for the community.
This could represent a more organic and decentralised approach to city equipment design in which physical infrastructures not only represent existing communities, but help to create and strengthen those communities at an early stage.
There is abundant literature about the design of temporary structures in recent architectural history, but it reduces considerably when we narrow the search to design for self-build. For example, the geodesic structures designed by Richard Buckminster Fuller were not designed with self-builders in mind but their inherent lightness, strength and the use of small size components have made them extremely popular among self-builders of temporary structures all over the world. Also, the fascinating research on paper as a structural material developed by Shigeru Ban over the course of more than two decades has created a fantastic opportunity to consider paper as a plausible material for temporary self build.
Buckminster Fuller, the Whole Earth Catalog and the geodesic dome
Richard Buckminster Fuller was an American architect, engineer and philosopher born in 1895 and well known as the inventor of the geodesic dome. Fuller was very interested in high-strength-to-weight designs, environmentally sustainable with minimum use of resources. One of his fields of work was the development of a system for building temporary domes applied to shelters, greenhouses and trade fairs. The United States Pavilion at Montreal’s Expo 1967 is an outstanding example; a three- quarters measuring a sphere of 76 m in diameter and 60 m height.
Geodesic domes became extremely popular among self builders during the 60’s and 70’s with dozens of Do-It-Yourself publications and step by step manuals. The Whole Earth Catalog and the latter Domebook are outstanding examples of this period which compiled vast amounts of practical information on how to self build geodesic domes with a wide rage of materials and construction methods.
Paper buildings by Shigeru Ban
Shigeru Ban is a 58-year-old Japanese architect awarded with the Pritzker Architecture Prize in 2014 for his work on building temporary emergency shelters and facilities using recycled cardboard tubes. He has done a lot of pro bono work in disaster zones by building temporary homes and schools for the homeless survivors of earthquakes and genocides, such as the temporary Takatori Catholic Church built after the earthquake in Kobe 1995 and the paper emergency shelters for Byumba Refugee Camp in Rwanda 1999. In many of these cases the system has been developed specifically with self builders in mind. The use of paper is determined by its low cost, recyclability, low-tech and replaceable capabilities. Ecological architecture and humanitarianism are key aspects in Ban’s work. Later, Ban has also introduced paper as a structural material in permanent public buildings and villas.
Community innovation hubs
Innovation in building technology in the past decades has been principally produced in formal research spaces such as industry laboratories, university departments and design offices. For this reason, innovations have tended to concentrate in the high end spectrum with sophisticated material developments and more efficient industrial processes. This approach has relegated self- build construction to vernacular methods and amateur informal research with almost no input from professionals or industry.
In recent years, new hybrid spaces such as hacker spaces and living labs are defining new innovation models in which formal and informal research blend together, and professional and amateurs share space and equipment. These new spaces are producing notable innovation in fields like energy production, computing and manufacturing as they put together research and the challenges of our societies. Fab Labs are becoming the best spaces for fostering innovation in building technology for communities as they are at the same time innovation hub and workshop space; research laboratory and community centre; manufacturing facility and local library. Architects and designers could participate in these new innovation hubs by envisioning systems based on low-cost materials using new fabrication technologies for simplified manufacturing and assembly by the end users themselves.

Fab Labs
Fabrication Labs are spaces for engineering and invention, allowing individuals to design and produce tangible objects on demand. Some of the tools that communities can find in a Fab Lab are CNC routers, laser cutters, 3D printers and electronics assembly capabilities. More important than the technology are the new ways of self-expression that a Fab Lab enables. Fab Labs are conceived as a community resource offering open access to the space, the equipment and adequate training. The real strength of Fab Labs grounded in their social consequences: decentralised and low-cost ways to make things can help building better communities.
In 2014, there are more than 270 independent Fab Labs in 70 countries around the world. To achieve the full potential of the maker movement, cross collaboration between different labs and types of users is needed. Fab Lab Limerick started in 2012 when students and lecturers began building their own 3D printers, CNC routers and laser cutters as part of the elective programme at the School of Architecture of the University of Limerick. In 2014, Fab Lab Limerick moved to an empty building in the city centre owned by Limerick City Council. Since then, the space offers, to everyone in the city a continuous cultural program, open access to digital fabrication tools and a broad range of tutorials and courses.
Fab Lab Limerick provides the community with flexible and high precision tools needed for scale prototyping and full size building. These computer controlled tools are no longer limited to R&D laboratories or mass production, digital fabrication technologies accelerate the process of invention and ideation giving back means of production to everyone, in other words, democratising advanced building technology.
Geodesic Domes
The Geodesic dome is a type of structure that meets many of the requirements for a self-build construction system. First, a geodesic dome is one of the strongest, lightest and most efficient means of enclosing space so it represents an extremely efficient and cost effective use of materials. Second, it works best when used to cover large collective spaces and compared to other long span structures, the construction elements are small and light enough to be assembled without auxiliary equipment like cranes or scaffolding.
The sphere is nature’s most efficient shape, covering the most area with least amount of surface. Additionally, geodesic domes constitute a special case of tensegrity structures in which each structural member is either in pure compression or pure tension with no structural member experiencing a bending moment. This means that the geodesic dome is not only the most efficient structure for its spherical shape but also because it replicates most effectively the tensional integrity of soap bubbles and sea shells skins.
Geodesic domes are mathematically derived structures and the mathematics required to describe them geometrically have not been widely available until recently. Moreover geodesic dome structures need to be fabricated much more precisely than traditional building construction methods so they normally have been relegated to mass industrialized manufacturing facilities or highly skilled and specialised crafts persons. Domestic digital fabrication technologies can overcome these obstacles and make geodesic domes more accessible to the general public and communities all over the world.
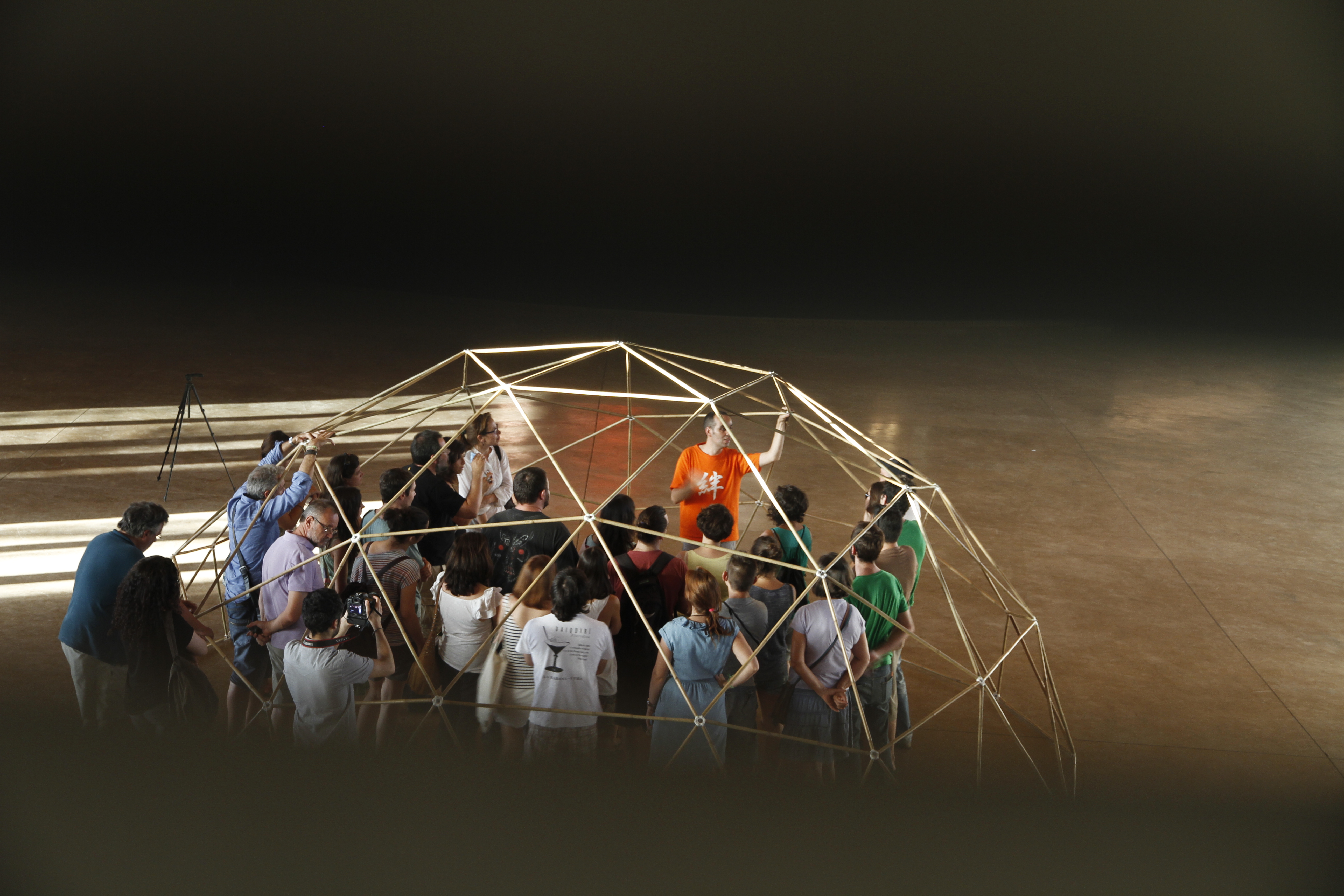
First prototype: bamboo and 3d printed dome
In the summer of 2013, colaborativa.eu developed a first prototype for temporary structures based on low-cost components and digital fabrication. This first geodesic dome was based in bamboo struts and 3d printed bio-plastic connectors. A small group of people with several 3D printers was able to print out the necessary connectors for a 6.5 meters diameter dome in just one day. The assembly was carried out by three people in less than two hours and the prototype had an approximate cost of 4€ per square meter.
Another advantage of this system is that both assembly and disassembly did not require specialised training and could be made collectively: the more people participating, the faster the assembly. The connectors were a design derived from the domekit.cc project by Effalo.com adapted to work with bamboo struts. The connector was based on a socket-ball design which allowed rotation on each strut correcting small differences in length and curvature. Since each ball was 3D printed instead of cast or injection moulded, the part could be adapted to each unique bamboo strut diameter. In the end this method proved too time consuming during the prototype development. A complete parametric design could facilitate this process and it has been considered by the authors for future prototypes.
Second prototype: Cardboard tubes and CNC router
In August 2014, colaborativa.eu partnered with Fab Lab Limerick, part of the School of Architecture University of Limerick, to develop a second iteration of the design. Following the same principles of low-cost and digitally fabricated, the second iteration used cardboard tubes and digitally fabricated plywood connectors. This change of materials allowed bigger for domes with a span of up to 14 meters and 150 square meters covered area.
Geodesic Geometry
The proposed design is based on the 3V 5/9 Fuller-Kruschke method. This method –developed by Buckminster Fuller in the mid 50’s and later described by David Kruschke in his 1970s book “Dome Cookbook of Geodesic Geometry”– is a more complicated variation of the 3-frequency geodesic division of the icosahedron. The Fuller-Kruschke method introduces a fourth length strut which generates a flat base making it very adequate for architectural applications as weight is evenly distributed through a circular flat base and its 15 vertices.
The 3V 5/9 Fuller-Kruschke method is formed by 165 struts of 4 different lengths, and 61 connectors. To determine the dome chord factors and angles –chord factors are numbers that when multiplied by the radius of the dome give you the length of a strut– several mathematical formulas described by David Kruschke were used as well as geometric projections using 3D modelling software. A complete mathematical model of the Fuller-Kruschke method would facilitate the geometric description of the structure and will be developed by the authors in future prototypes.
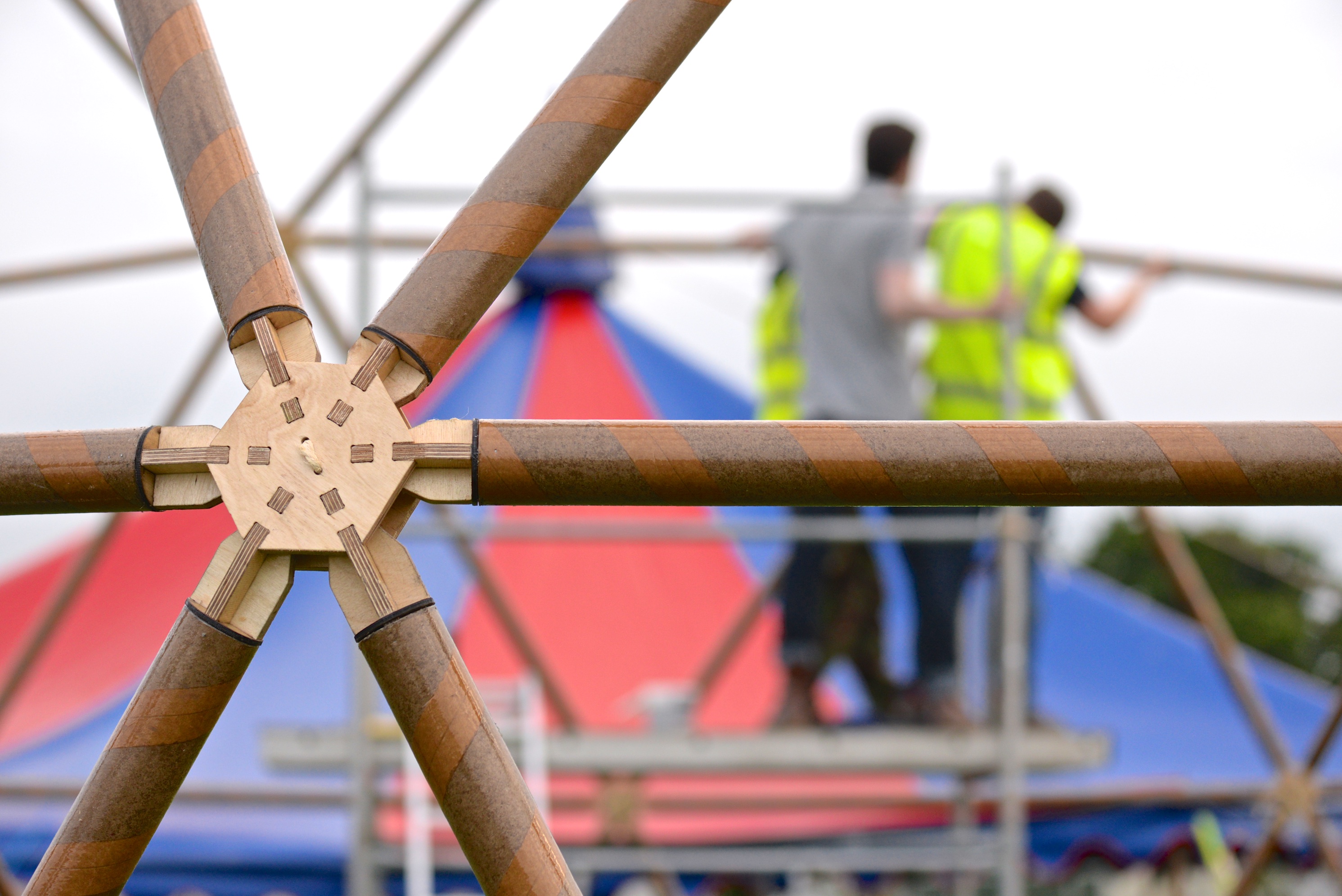
Materials
Paper tube is a construction material that has gained popularity since Japanese architect Shigeru Ban started to experiment with it at the end of the 80’s. Paper tube has been described by Ban himself as “evolved wood”. This material is easily available in many parts of the world and its manufacturing process does not require complex technology. Paper tube is manufactured from rolls of recycled paper that are cut into strips, saturated with glue, and wound spirally around a solid metal rod that creates the hollow core of the tube. Tubes can be made to any diameter, length and thickness, and used tubes can be recycled afterwards. For this second prototype and due to time constraints, tube diameter and wall thickness dimensions were based on Shigeru Ban’s emergency shelters from 1995. The authors recognise than a more analytical approach for the tube sections calculation is needed and they are currently working with the civil engineering department at the University of Limerick to devise a simple structural calculation model.
Paper tubes have great mechanical properties if they are kept with low moisture content –an increase of just 1% of moisture content produces a loss of strength of around 10%– therefore finding a viable method for waterproofing the paper tubes is crucial. A two step method was found in the paper “Portals to an Architecture: Design of a Temporary Structure with Paper Tube Arches” by Preston: first a moisture barrier ply is included below the first few paper layers, this waxy layer prevents moisture from penetrating deeper into the paper tube. This first step was not used on the prototype due to time constraints but this technical possibility is being discussed with an Irish manufacturer for future prototypes. The second step is to apply an external waterproofing layer of a low volatile organic compound polyurethane. A more environmentally friendly solution is being considered for the next iteration of the prototype.
A plywood hub detail, which differed greatly from the 3D printed ball-socket connector from the first prototype, was developed based on two principles. First, it had to be able to be rapid prototyped using laser cutting so each design iteration could be cut and tested at 1:1 scale as quickly as possible. Second, the hub needed to support the position of the paper tubes rigidly during the assembly process as the whole system was meant to be assembled without the need for auxiliary structures such as cranes, scaffoldings or additional supports.
A flat-pack two-parts joint was developed, this detail is loosely based on Shigeru Ban’s roof detail for the Paper Log Houses built after Kobe earthquake of 1995. One part has a cross section and it is attached at the end of the paper tube; the other consists of two plates connected with a twisting rope tensor which clamps the tubes together locking them into place. Twelve millimeters furniture grade Birch plywood was selected over solid timber for cost and ease of manufacture. The design evolved rapidly in a five day period thanks to very quick iterations using 6mm hardwood faced plywood prototypes layered together.
Conclusions
The final prototype was successfully assembled at the Global Green area during 2014 Electric Picnic Music Festival.The prototype stood rain and adverse climate conditions with no apparent loss of structural strength although further tests in a more controlled environment need to be carried out to ensure stability in the long term. Additionally, structural analysis of the dome and finite element simulations for the connectors will be required to adjust paper tube sections and connector dimensions.
Finally, a skin solution based on low cost materials and digital fabrication manufacturing is required to be developed before the design can be used as a temporary structure for communities. A third prototype of 14 meters of diameter and covered with an inflatable transparent skin and a solid base is planned to be prototyped and manufactured this summer 2015 at Fab Lab Limerick. This prototype is the first step towards a complete construction system which will allow communities to independently design and fabricate collective enclosed spaces based on geodesic structures without any later intervention by the designer. The next steps will be releasing the construction system under an open source license, allowing for further improvements and more flexibility to the system, as well as developing a software tool which will facilitate end users to customise the geometry and cut all the necessary parts in any Fab Lab equipped with a CNC router. The authors believe that full-scale structural systems using Fab Labs for both rapid prototyping and manufacturing could open up innovation in building technology to communities all around the world.
Acknowledgments
Stephen Bourke, Jack Byrne, Aoife Marnane and Jennifer O’Riordan, all graduates from the School of Architecture University of Limerick, took part in the design and manufacturing stages of the second prototype. The dome was assembled at the Electric Picnic by Michael McLaughlin, Aidan Byrne, Stephen Bourke, Jack Byrne, Aoife Marnane, Jennifer O’Riordan and Javier Burón. The authors are grateful to Global Green and WeCreate for inviting us to assemble the prototype at their show area at the 2014 Electric Picnic.
Article published in the first issue of Iterations Journal, you can find the original article in PDF here: Iterations 01